About us
Sustainability
With our photovoltaic system in combination with effective building insulation, we can generate our own energy and use resources efficiently. All company cars are electric or hybrid vehicles. We also offer our visitors this state-of-the-art charging infrastructure. We reduce internal paper and resource consumption through a high degree of digitalisation. Our company bike leasing scheme, which has been well received by colleagues, has already saved a number of car kilometres. In this way, we are jointly reducing CO2 emissions.
Social commitment
As a responsible company, we are actively involved in social and charitable projects. Supporting young people is particularly important to us. That's why we support regional schools to inspire young technical talent at an early age and work together with educational institutions. We are also committed to local sport by supporting regional clubs and thus making a contribution to sporting development and the community. Our aim is not only to be economically successful, but also to strengthen the region in the long term.
Education
We are a mechanical engineering company with a clear focus on innovation and precision. Our range of services includes the development, design and manufacture of high-quality machines and technical solutions for various industrial sectors. We offer apprenticeships in the professions of technical product designer and electronics technician and provide in-depth specialist knowledge and practical experience in a modern working environment. Our trainees benefit from intensive support, exciting projects and excellent development opportunities. Interested parties can apply at office@mbs-ac.de contact us.
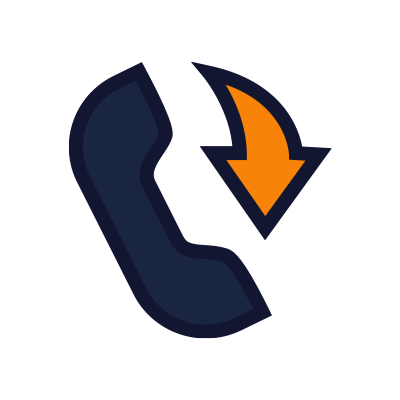
Service
02404-95840-132
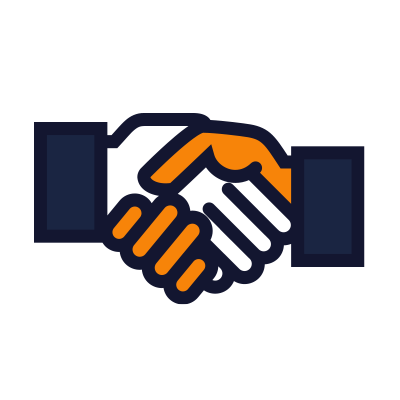
Distribution
02404-95840-10
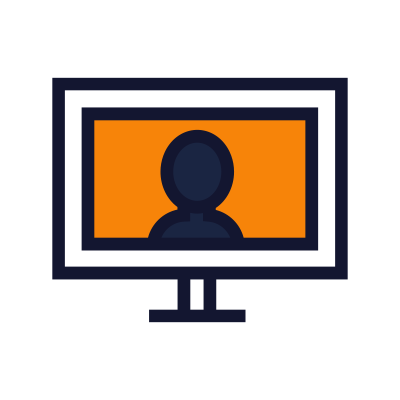
Office
02404-958-131